Planet – production and the environment
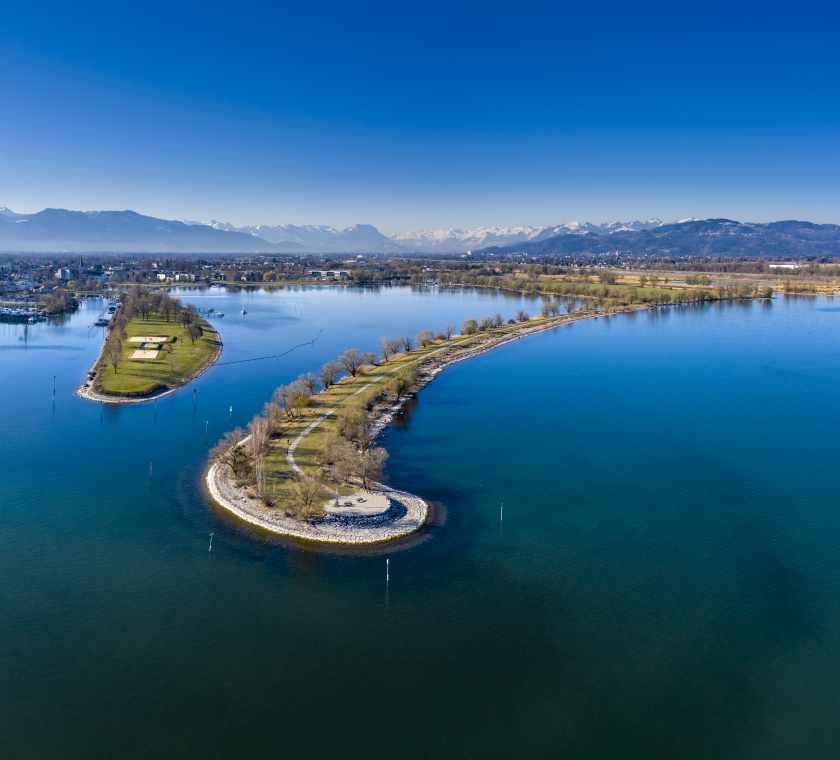
As a manufacturing company, ALPLA is reliant on resources such as energy, gas, fossil-based raw materials and water. We are aware of how important it is to the future of the planet and to future generations that we use these resources efficiently. We understand efficient use to mean getting as much as possible out of the raw materials. We wish to use them wisely and keep them within the material cycle. The professional collection and recycling of plastics prevent them from polluting the environment and being harmful there.
Production energy efficiency
Energy has a key part to play in the production journey from the raw material to plastic packaging. We at ALPLA attach maximum importance to using energy efficiently and responsibly. For ALPLA, a state-of-the-art infrastructure is the key factor when it comes to energy management. A dedicated team conducts annual plant energy assessments at selected sites. Following a successful assessment, there is savings potential of around 10%. Much of the savings are made possible by the modernisation of and investments in new systems and machinery.
‘Energy efficiency is more important than ever in order for us to meet our ambitious sustainability targets and reduce the risk of volatile energy prices.’
Andre Alber, Corporate Plant Engineer
Renewable energies
Using renewable energies in production is very important as this contributes to environmental protection, conserves resources, drives innovation and meets the customers’ needs. By making increased use of renewable energies, ALPLA can do business sustainably and help create a liveable future.
We have a clear goal of gradually increasing the proportion of renewable energies we use – this is in line both with customer demand and with our decarbonisation efforts. We already have plants which are operated entirely or almost entirely on renewable energies in countries such as Austria, Germany, Spain, Portugal, Poland, Mexico, Costa Rica and Panama, and we are actively looking into increasing our proportion of renewable energies further around the world. This includes short-term initiatives to switch to 100% renewable energy from biomass at more plants in the UK as well as to source 70% of our energy at the remaining plants in Germany through power purchase agreements (PPAs) from 2023. In addition to the 70% of energy from PPAs in Germany, we have secured energy attribute certificates (EACs) for the remaining 30%, meaning all of our German plants will be run entirely on renewable energy from 2024.


Materials management
Modern technologies and sophisticated design keep packaging weight as low as possible. This allows us to reduce material consumption and costs – and conserve fossil resources. To achieve this, we at ALPLA work closely with our suppliers, research institutes and customers. ALPLA also has decades of experience in the production of recycled plastics and processing them into new packaging.
Our experts additionally work with plastics from renewable resources, otherwise known as bio-based plastics. Here, we also consider factors such as competition with the food industry for these materials and also their recyclability. ALPLA does not use materials and substances that are harmful to the environment, such as PVC, plasticisers and heavy metals.
Greenhouse gas (GHG) emissions
We at ALPLA are mindful of the fact that our business activities contribute to the global carbon equation. We therefore regularly quantify our carbon footprint related to the production of plastic packaging and recycled materials. The metric we use for this is CO2e. In addition to carbon dioxide, this also includes other greenhouse gases which are converted into carbon dioxide quantities on the basis of their climate impact.
‘The path to decarbonisation calls for sound bases – our comprehensive GHG inventory ensures that we have a clear understanding of our basic plan emissions, as a starting point from which to be able to gradually reduce our global carbon footprint.’
Miklos Toth, Head of Sustainability
In 2023, we conducted a comprehensive calculation of the carbon footprint attributable to our production (Scopes 1 and 2) and our value chain (Scope 3) in 2021 and 2022, in line with the requirements of the Greenhouse Gas Protocol. This affords us clarity regarding the starting point of the decarbonisation path we must follow.
- Our Scope 1 GHG emissions comprise stationary combustion (natural gas and oil, used in many cases for heating), mobile combustion (our vehicle fleet’s fuel consumption) and fugitive emissions (refrigerant losses within our cooling systems). However, these emissions are negligible in comparison to the total greenhouse gas emissions.
- Our Scope 2 GHG emissions from electricity consumption account for a considerable proportion of our total GHG emissions. We calculate both the location- and market-based emissions in order to obtain a differentiated view of our impacts as we switch over to renewable energies, this being the most important decarbonisation lever when it comes to Scope 2 GHG emissions.
- Scope 3 GHG emissions account for almost 90% of our total GHG emissions. The category ‘Purchased goods and services’ is by far our biggest Scope 3 category (accounting for 75%) as we are dependent on raw materials for our plastics processing business and on post-consumer bottles for our recycling activities.
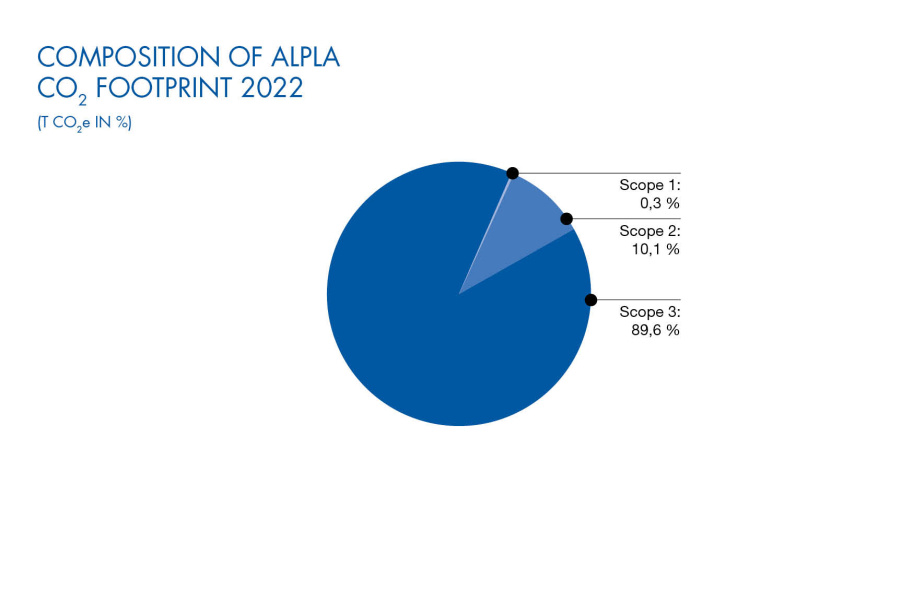
CO2 calculation and certificates
We are happy to help our customers develop sustainable packaging solutions. We calculate our products’ carbon emissions based on the current regulations and issue corresponding certificates.
We would be happy to advise you, ideally in a personal consultation. Please contact our Sales team or the ALPLA Sustainability Management department: sustainability@alpla.com.
Water and waste management
Although our packaging production involves only little water consumption (water has greater significance in our recycling processes as it is used to wash the feedstock), we are aware of the importance of water as a vital resource and endeavour to use it efficiently and responsibly. We obtain (fresh) water primarily from municipal sources and, at a number of our facilities, from our own systems. This combination of water sources helps us maintain a continuous supply while also taking local water availability and sustainability into account.
We endeavour to comply with all the relevant regulations and standards regarding water usage and precisely monitor the quality of the water we use and discharge in order to prevent negative impacts on the environment or the people in the vicinity of our plants. We perform regular checks and tests to ensure that our water consumption is in line with the established guidelines.
We recently developed our water stress analysis with the World Resources Institute’s Aqueduct tool in order to map water stress at our sites. We came to the conclusion that around 50% of our water withdrawal is from areas with high or extreme water stress (i.e. the water requirements exceed the local supply by at least 40%). Also, 44% of our sites are located in areas with high or extreme water scarcity. The countries most heavily affected are Mexico, India, Italy, Spain and Turkey.
‘WATER IS ONE OF THE MOST PRECIOUS RESOURCES IN THE WORLD. DRINKING WATER IN PARTICULAR IS SCARCE IN MANY REGIONS. ALPLA THEREFORE PROMOTES THE MINDFUL AND ECONOMICAL USE OF WATER.’
Linda Staib, Senior Sustainability Manager
Our waste management during operations likewise reflects our focus on the circular economy. All the plastic waste that occurs during production is recycled and subsequently fed back into the material cycle. We also sell material waste that cannot be recycled within our production process. When collecting data at our plants, we distinguish between special waste (cleaning chemicals, oils, batteries, paints, etc.) and non-hazardous waste (municipal waste, packaging waste, construction and demolition waste, etc.).
ALPLA additionally signed up to the Zero Pellet Loss (ZPL) initiative in 2013 to minimise the loss of small pieces of plastic at our plants. Pellets are small beads of raw plastic that can easily disappear down cracks or behind machinery or get stuck in the soles of workers’ shoes. They then find their way into the environment or into bodies of water. All kinds of measures have been developed and introduced to prevent this, such as custom-built vacuum cleaners, collection systems in silos and tailored wastewater sifters. Our staff are also given special training in order to prevent pellet loss.